Slagging and Fouling.
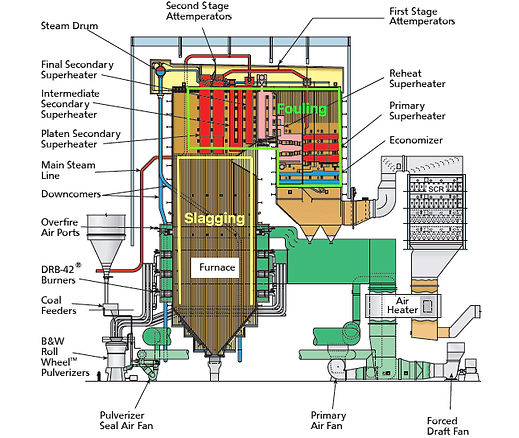
Slagging and fouling is a major operational concern for coal-fired power plants, resulting in reduce power generation, and increased shutdowns and maintenance. Slag is molten ash and incombustible by-products that remain following coal combustion and can stick to furnace components. Fouling refers to deposits that occur in the convection pass after the gases exit the furnace, and is generally caused by ash cinders and accumulations that form on the leading edges of the super heater and reheater tubes.
Ash with low melting temperatures causes these slagging and fouling problems in pulverized combustion boilers. Ash deposition on the heat exchange tubes affects the decrease in the overall heat transfer coefficient due to the thermal conductivity of the ash as well as several other operation problems. Ultimately, deposits in the high-temperature zone lead to corrosion, reduced heat transfer, and shortened equipment life.
Fuels with extremely high fusion temperatures are considered to be boiler-friendly and forgiving, while fuels with lower ash fusion temperatures require more precise combustion tuning and increased soot blowing to mitigate slag deposits. The catalyst minimizes the potential for corrosion and reduces slagging and fouling on the boiler super heater tubes. By increasing the fusion temperature of the ash, the little fouling that still occurs is dry, friable, and an easily removed deposit instead of the wet and sticky slag that leaves a rock hard coating on the tubes.
In dry bottom boilers, the wall slag changes from sintered to vesicular or amorphous and can run down the wall, plugging the opening at the bottom of the furnace. Wall slag acts as an insulator and impedes heat transfer to the water wall, which increases furnace gas exit temperature and allows molten particles to escape the furnace where they can cause slagging of the screen tubes and convection passes. Slag buildup around burners can occur, blocking the coal flow into the furnace. This can result in combustion taking place behind the burner, causing damage to the burner, wind box, and coal pipe.
Merely 1mm of bonded deposit on metal walls will reduce heat-transfer from fire to water by up to 10%. The catalyst burns the vaporized tars instead of allowing them to coat the tube walls, so that no additional coal is required to maintain a constant heat transfer over extended periods.
One of the prevailing causes of slagging and fouling is secondary combustion at the upper furnace. The most common cause of secondary combustion is insufficient excess oxygen within the burner belt. When coal ash has an iron content of over 10%, the melting temperature of the ash is lower in a reducing atmosphere. If the coal ash contains significant amounts of iron, the fusion temperature can be drastically lower as a result of the ash chemistry. Consequently, the ash will melt at a much lower temperature in a reducing atmosphere from what the fusion temperature would be in an oxidizing atmosphere. This can be particularly serious for eastern U.S. plants that burn bituminous coal.
Source of Slagging and Fouling "Typical Causes of Slagging and Fouling Problems in Boilers" by Richard F. Storm http://www.powermag.com/typical-causes-of-slagging-and-fouling-problems-in-boilers/?pagenum=4